Dismiss Notice
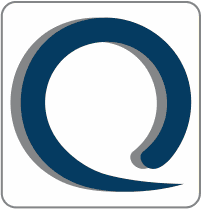
You must be a registered member in order to post messages and view/download attached files in this forum.
Click here to register.
Click here to register.
7.2 Competence: How much documentation is needed?
Discussion in 'ISO 9001:2015 - Quality Management Systems' started by John Apostoli, Sep 20, 2016.
Tags: