Dismiss Notice
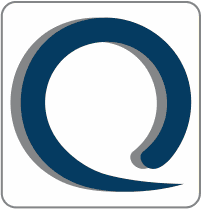
You must be a registered member in order to post messages and view/download attached files in this forum.
Click here to register.
Click here to register.
7.1.5.2.1 Calibration/verification records
Discussion in 'IATF 16949:2016 - Automotive Quality Systems' started by Josepi, Aug 7, 2018.