Dismiss Notice
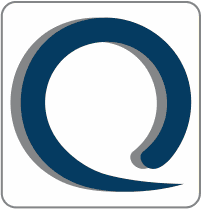
You must be a registered member in order to post messages and view/download attached files in this forum.
Click here to register.
Click here to register.
Can a company get ISO/TS 16949 even if no customer requires it?
Discussion in 'IATF 16949:2016 - Automotive Quality Systems' started by alltrees, Nov 24, 2015.
Page 1 of 2
Page 1 of 2