Dismiss Notice
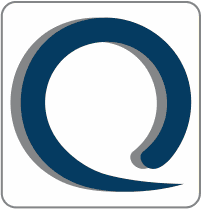
You must be a registered member in order to post messages and view/download attached files in this forum.
Click here to register.
Click here to register.
S chart Upper control limit
Discussion in 'SPC - Statistical Process Control' started by Jackson Yeo, May 14, 2024.