Dismiss Notice
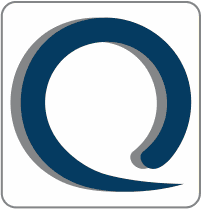
You must be a registered member in order to post messages and view/download attached files in this forum.
Click here to register.
Click here to register.
To understand in what all ways we integrate the third-party manufacturer under QMS of organization
Discussion in 'ISO 9001:2015 - Quality Management Systems' started by Rajan Gupta_07, Mar 26, 2024.