Dismiss Notice
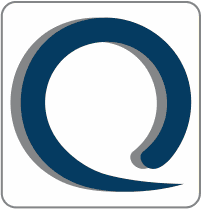
You must be a registered member in order to post messages and view/download attached files in this forum.
Click here to register.
Click here to register.
Managing Clause 9.1.1. for Documenting Inspection Results
Discussion in 'IATF 16949:2016 - Automotive Quality Systems' started by qmr1976, Jan 10, 2024.