Dismiss Notice
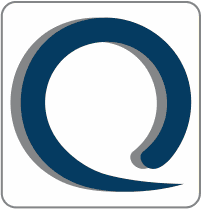
You must be a registered member in order to post messages and view/download attached files in this forum.
Click here to register.
Click here to register.
No Quality Manual, now what?
Discussion in 'ISO 9001:2015 - Quality Management Systems' started by Andy Nichols, Aug 28, 2015.
Page 2 of 5
Page 2 of 5