Dismiss Notice
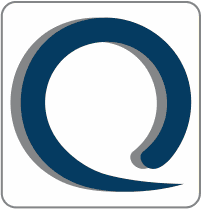
You must be a registered member in order to post messages and view/download attached files in this forum.
Click here to register.
Click here to register.
Injection Molding Company Compliance Manager seeking help with prep for external cert audit
Discussion in 'ISO 9001:2008 - Quality Management Systems' started by PeteWizkid, Jul 21, 2016.