Dismiss Notice
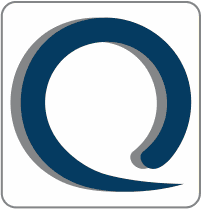
You must be a registered member in order to post messages and view/download attached files in this forum.
Click here to register.
Click here to register.
Recalculate control limits for every lot?
Discussion in 'SPC - Statistical Process Control' started by Jennie, Jan 21, 2016.
Page 1 of 2
Page 1 of 2