Dismiss Notice
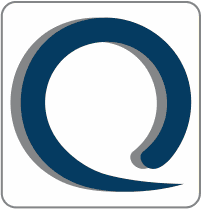
You must be a registered member in order to post messages and view/download attached files in this forum.
Click here to register.
Click here to register.
QMS and Compliance KPIs
Discussion in 'AS 91XX - Aerospace Quality Standards' started by ISO9001TD, Jun 18, 2022.