Dismiss Notice
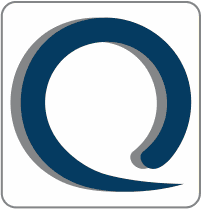
You must be a registered member in order to post messages and view/download attached files in this forum.
Click here to register.
Click here to register.
When does Research become Development?
Discussion in 'ISO 9001:2015 - Quality Management Systems' started by Graham Thorpe, Feb 25, 2019.